From Sketch to Reality: Bringing AGS Stainless Products to Life
Just how does AGS Stainless transform an initial idea into a custom-fabricated railing system that distinguishes a building or interior space?
It typically begins with a simple sketch.
From this initial concept, our sales department will develop a cost estimate for review. Once approved, the job will be assigned to one of our designers, who will transform the sketch into a CAD drawing that includes specific point-to-point dimensions.
After the CAD drawing gets the green light, the job goes into fabrication. Because we stock all raw materials in our warehouse, we are able to quickly bring the concept to life.
Cutting the post and top rail material to length is the first stage of fabrication. We use a state-of-the-art laser tube cutter to guarantee precision and quality.
Once the product is cut to size, the laser drills the holes for the infill at the proper size and angle. Everything is automated to ensure consistent quality.
Next, all components come together at welding stations, where our welders pride themselves on precise craftsmanship. AGS Stainless welds all its railing system components by hand, allowing the attention to detail craftsmanship of our product to shine through at each and every joint.
After welding, everything is hand polished and all welding stains are removed. The order then moves to our shipping department. We package everything to protect the stainless steel so there won’t be any scratch marks or gouges when it arrives at its final destination. Jobs are shipped using UPS, FedEx or whichever carrier our customers prefer.
In the end, AGS wants to make the process of selecting, designing and installing railing systems as easy as possible for our customers. Watch the video below to get an inside view of the AGS offices and see the behind-the-scenes manufacturing process.
About the Author
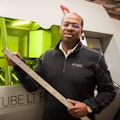
Kevin T. Harris
Since 2013 Kevin Harris has served as Director of Sales & Marketing for AGS Stainless, Inc. Mr. Harris has an extensive track record in business development, marketing, communications and sales. Prior to his position with AGS Stainless, Mr. Harris founded 4 industry-leading firms including 2-information technology firms, one specializing in the creation of web-based process management tools for Fortune 100 corporations and one that specialized in building predictive modeling applications for federal agencies, a real estate development firm that spearheaded the restoration and redevelopment of a historic seaport communities downtown waterfront and a state-chartered community bank. Two of these four companies he sold to publicly traded corporations.